7 Ways to Maintain your Drilling Equipment Between Jobs
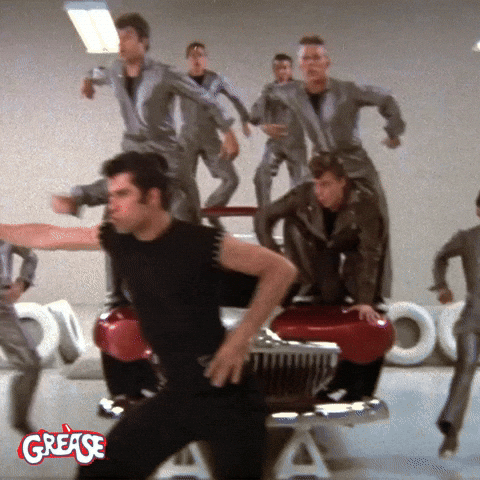
1. Grease
Your drill has many grease points that prevent early wear and allow your machine to run smoothly. Regular greasing is important to maintain the machine during use. Sometimes, when your drill is doing work on the job site, common grease points are overlooked during daily maintenance. Down-time on the job site provides a great opportunity to look over your machine closely and make sure everything is well greased.
2. Set Chain Tightness
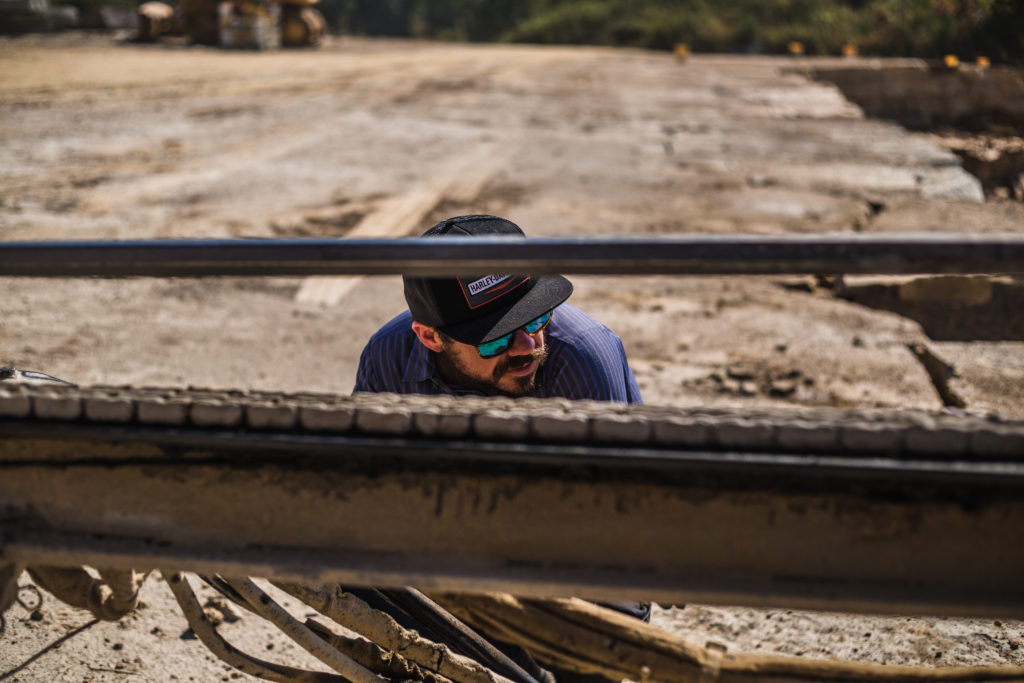
The feed rail chain on your WORD Rock Drill can become loose periodically. The natural movement of the machine during drilling leads to wear within the primary sprocket of the feed rail chain. This sprocket contains a 1/16th brass bushing which is often the cause of a loose chain. When testing your chain tightness first check to make sure the brass ring within the sprocket is in place and not showing signs of wear. You can then proceed to tighten the chain as usual. Test the tension by moving the drifter all the way forward and checking the rigidity at the middle of the chain.
3. Check Your Lubricator
During your down time it is important to make sure your line oiler is refilled with rock drill oil. When drilling, the oil level in your line oiler should be checked twice a day. When checking your line oiler between jobs, perform the white paper towel test to make sure that oil is making its way through the unit.
4. Clean Quick Connects
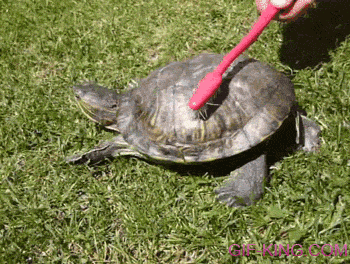
No job site is clean, so it is almost impossible to prevent your quick connects from getting dirty even when they are hooked up. Although they pretty much stay dirty, it’s important to clean the quick connects when re-attaching them to your machine. With the combination of hydraulic oil and dirt, they can get pretty grimy between uses and you don’t want that dirt to make its way into your hydraulic line.
5. Check Extension Clamp Plates

The extension clamp plates are protective plates located on your feed rail. These plates serve as a buffer between the steel of your feed rail and the steel of your feed rail extension piece. The use of these plates prevents the two sections of feed rail steel from grinding together during movement. As the clamp plates wear down, you will notice that the feed rail extension will jostle more when being extended and moved.
6. Check Nylatron Wearpads
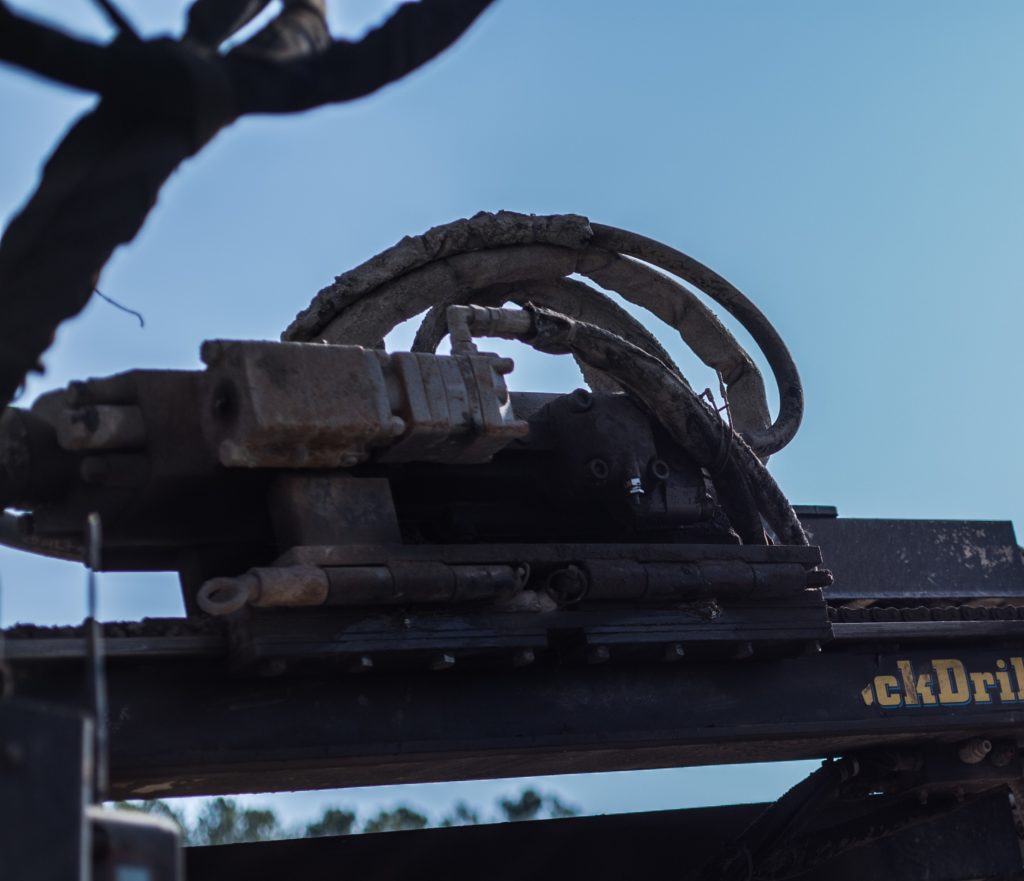
Located on the mounting assembly for your Word Rock Drills motor, the Nylatron Shims on your rock drill allow your motor to move smoothly along your feed rail. Over time, these Nylatron Wearpads become thin due to the constant movement. Regularly replacing these wearpads is essential for maintaining the longevity of your machine.
7. Look for Wear on your Centralizer Gates
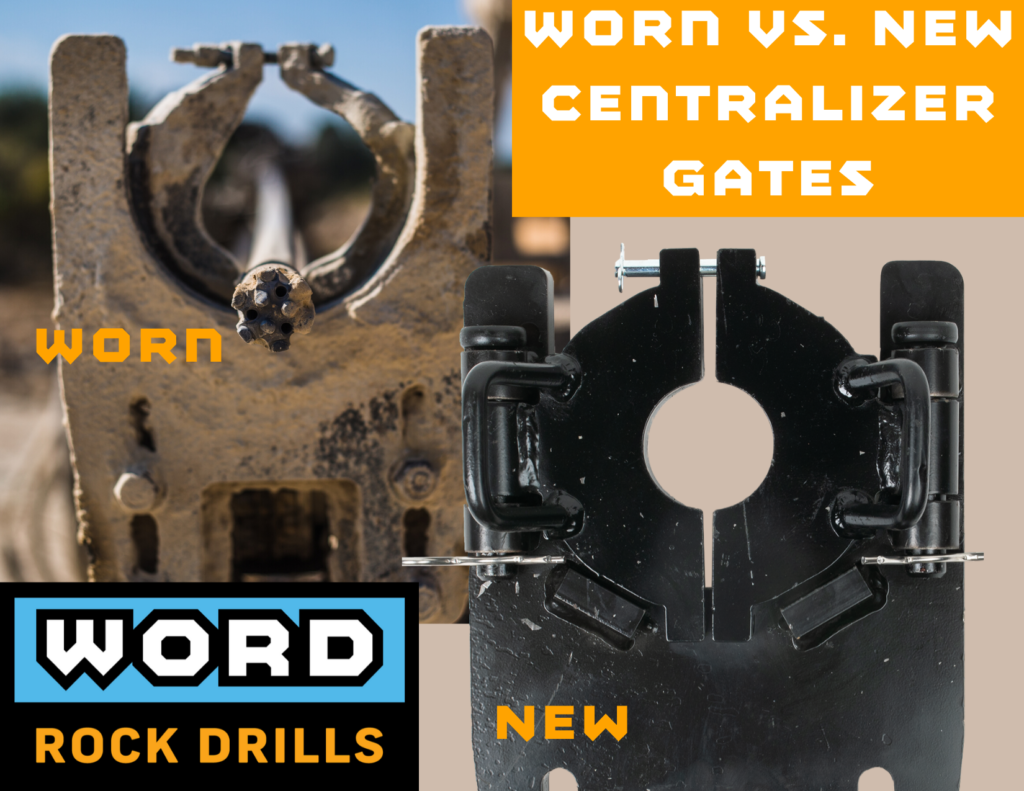
As a key component in the movement of the drill, your centralizer gates wear down throughout a job. Check your centralizer gates between jobs and replace them when they start to wear down to keep your machine in peak condition.